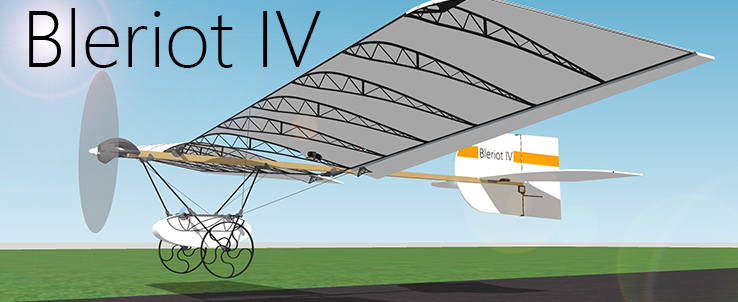
Die Story:
Die
Bleriot III von Ikarus hat uns mehr als 15 Jahre lang Freude bereitet
(siehe Bleriot III), doch
hat sich das Glück gewendet und meine Vertigo
hat in der Luft bei einem großen Looping eine Flächenhälfte der Bleriot
mit dem CFK-Fahrwerk geteilt.
Der
Zufall wollte es, dass der Crash aus der Luft von der zweiten Bleriot
festgehalten wurde (Klick aufs Bild für Video):
Die
Vertigo konnte unversehrt landen; die Bleriot trudelte unsteuerbar zu
Boden. Der Schaden war zwar nicht hoch, jedoch war der Wind stark
genug, um die abgeschnittene Fläche einfach wegzutragen - so lange, bis
wir sie aus den Augen verloren...
Da
das Wiesenschleichen und Zeitlupenlanden am Feldweg zu unseren
liebsten Flugerfahrungen zählt, hab ich beschlossen, die Beriot wieder
flugtüchtig zu machen.
Leider ist die Bleriot III von Ikarus schon seit 10 Jahren nicht mehr
erhältlich (was ich für einen schweren Fehler halte, da das Modell -
verglichen mit dem vielen anderen Plastik-Schrott, der heute verkauft
wird - wirklich herausragende Qualitäten hat: Beherrschbarkeit,
Erlernbarkeit, niederige Fluggeschwindigkeit, reparaturfreundliches
Design etc.) und so gibt es auch keine Ersatzteile.
Die Herausforderung liegt nun in der Formgebung der Fläche, die von
Ikarus aus gefärbtem Polystyrol in einer Form geschäumt wurde. Zwar ist
die Fläche gleichmäßig 3mm dick, aber das "Profil" weist einen
deutlichen S-Schlag aus, sodass man mit einer einfachen gewölbten
Platte das Ziel nicht erreicht.
Der erste Versuch:
Aus
Sperrholz hab ich zwei Gerüste bestehend aus Rippen und Nasen- und
Endleiste - jeweils für die obere und untere Kontur der Fläche -
erstellt. Zwischen diesen beiden Gerüsten wird nun eine 3mm
Depron-Platte eingklemmt und mittels Heißluftföhn vorsichtig erhitzt,
sodass das Depron "weich" wird und beim Abkühlen in "Form" bleibt.
Durch die Rippen soll die Struktur ähnlich der original Fläche
aussehen, und auch das S-Schlag Profil sollte dem Original gleichen.
So weit die Theorie.
Die Realität hat dann zwei richtige Probleme an den Tag gebracht:
- Die Profiltreue ist zu gering.
Das heißt:
nach der Entnahme der Depron-Flächen aus den gerüsten war
die Wölbung der Fläche deutlich geringer als die der Sperrholzrippen.
- Spannungne
in den Flächen. Das heißt: durch die ungleichmäßige
Erwärmung und Abkühlung der Flächen haben sich Spannungen aufgebaut,
die dazu führen, dass die Fläche bei leichten Verwindungen "umspringt"!
Sprich: es gibt zwei stabile Zustände, in der die Fläche verbleibt,
wenn man nach dem Verwinden loslässt. Das ist für eine Tragfläche
natürlich untragbar. Die Abspannung mit Angelschnur hat hier auch keine
Linderung gebracht, da die Verwindung in den äußeren zwei Dritteln
stattfindet.
Fazit zum ersten Versuch:
Ja, man kann die Maschine damit fliegen, aber die Flugeigenschaften
leiden gewaltig: Der Langsamflug ist viel anstrengender, da die
Maschine deutliche Tendenzen zum Ausbrechen hat. Die Gutmütigkeit ist
weg. Macht irgendwie nicht so richtig Spaß, weil der Pilot nicht mehr
steuert, wohin die Maschine fliegen soll, sondern die ganze Zeit nur
das ausbessert, was die Maschine nun falsch gemacht hat...
Darum
hab ich zu Beginn der Weihnachtsferien den Beschluss gefasst, die
Fläche komplett auf Basis einer anderen Konstruktion neu aufzubauen:
Der zweite Versuch:
Diesesmal
hab ich einen ganz anderen Ansatz gewählt und dabei gleich ein ganz
neues Modell konstruiert. Da die Unterschiede zum Ikaurs-Modell nun
größer sind, nenne ich sie auch Bleriot IV.
Hier die Auslegungsgrundlagen:
- Flächenspannweite
und Geometrie ähnlich der Bleriot III
- Profil:
gewölbte Platte - und anstelle des
S-Schlags noch angeflanschte Querruder, die auch als Flaps nach unten
gefahren werden können
- Höhen-
und Seitenleitwerksgeometrie ähnlich der
Bleriot III, aber geringfügig vergrößert
- Rumpf
wie bei der Bleriot III aus einem 10x10mm
Balsastab, aber 5cm länger
Features:
Naja, wenn man schon ein Modell komplett neu konstruiert und baut, dann
kann man ja auch noch ein paar Nachteile des Orignals ausmerzen. Zu den
Nachteilen der Bleriot III gehören unter anderem das "sperrige" Design
- sprich der Rumpf brauch beim Transport durch die fixen Streben,
Gondel und vor allem das Leitwerk viel Platz - und kann dadurch auch
leicht beschädigt werden. Darüber hinaus hat mich die Verspannung des
Leitwerks und die außen geführte Anlenkung des Höhen- und Seitenruders
gestört. Unpraktisch für den Start aus der Wiese war auch die
Fahrwerksachse, die gnadenlos bremst...
Hier nun die neuen Wünsche:
- Abnehmbares
Seitenruder und ins Seitenleitwerk integriertes Servo
- Komplett
abnehmbares Höhenleitwerk mit Servo im
Höhenleitwerk
- Abnehmbare
Gondel für den Akku
- Komplett
abnehmbares Fahrwerk
- Verschraubte,
austauschbare Steckung der Flächen
Konstruktion:
Neben dem Balsastab
für den Rumpf, besteht das ganze Modell noch aus Depron für Flächen
und Leitwerk, aus 2mm
CFK-Stäben für Flächenvorderkante, Endleiste,
Fahrwerksstreben und Verstärkungen des Seiten- und Höhenruders.
Räder,
Ruderhörner, Motorträger,
Verbindungselemente für die Streben, Verschlüsse und die Rippen für die
Flächen kommen alle aus dem 3D-Drucker.
Somit hab ich das gesamte Modell in 3D
mit der Software SketchUp konstruiert und dabei sind dann auch gleich
direkt die einzelnen Komponenten für den 3D-Drucker "druckreif"
entstanden: |
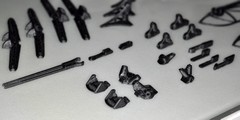 |
Bau:
Die Teile für den 3D Drucker hab ich mit einem Turnigy Fabrikator
hergestellt. Als Material verwende ich eine spezielle PLA-Mischung, die
mit 20% Carbon versetzt ist, sodass dei 3D-Teile gegenüber normalem PLA
die doppelte Festigkeit besitzen. Ausgenommen davon sind die Räder, die
habe ich mit normalem, schwarzen PLA gedruckt, weil die dürfen bzw.
sollen ja auch gut einfedern.
Begonnen hab ich mit den Flächen:
am Baubrett wird ein Raster im 10cm Abstand aufgemalt; die Rippen
werden mit dickflüssigem Superkleber an den 2mm Kohlestab vorne und
hinten geklebt.
Danach wird die Position der Rippen auf die Depron-Platte übertragen
und für jede Rippe erfolgt ein kleiner keilförmiger Einschnitt am
Depron, damit das Depron einerseits bündig mit dem Carbonstab
abschließen kann und andererseits nach ca. 1,5-2cm mit seiner gesamten
Stärke auf der Rippe aufliegen kann.
Auf der späteren Flächenoberseite wird am Depron nun mit 50%
überlappung ein 5cm breites, transparentes Klebeband aufgebracht (also
nur eine Hälfte des Klebebands ankleben, der Rest steht noch frei ab),
danach auf die Fläche an der Vorderkante und auf den Kohlestab UHU-Por
auftragen, trocknen lassen und dann so zusammenkleben, dass die
restlichen 50% des Klebebandes um den Kohlestab herum geführt werden
können und auf der Unterseite der Depron-Fläche angeklebt werden
können. Hierzu sollte man bei den Rippen das Klebeband jeweils mit der
Schere etwas einschneiden.
Nun wird die Kontur der Fläche noch zugeschnitten: die Ausformung des
Randbogens (abgeschnittenes Teil nicht wegwerfen - wird als Schablone
für die zweite Fläche verwendet, damit es schön symmetrisch wird) und
der genaue Zuschnitt der Flächenhinterkante.
Die selbe Klebe-Prozedur wie vorhin erledigt man an der
Flächenhinterkante: Rippen anzeichnen, Keile aus dem Depron
auschneiden, Klebeband, UHU-Por auftragen, trocknen, zusammenfügen,
Klebeband einschneiden und umklappen.
Und schon sind die Flächen fertig!
Der Rumpf
aus dem 10x10x850mm Balsastab - der je nach Balsa-Qualität 13g oder
auch mal 23g wiegen kann - wurde von mir an der Oberseite mit ein paar
wenigen Aramid-Rovings belegt und dann dünn mit UHU Endfest 300
eingestrichen. Das ist eig. nicht nötig, aber UHU Endfest 300 wollte
ich sowieso für die Verklebung des Motorträgers verwenden und da die
Kräfte ein wenig mit Rovings einleiten. Speziell beim Motorträger wäre
ein Verklebung mit Superkleber nicht ideal, da bei einer höheren
Belastung einfach ein paar Balsa-Fasern mitsamt dem Motorträger
abspringen. Also besser mit UHU endfest mit Föhn heißmachen, porentief
auftragen und mit Roving sichern.
Auch die zweiteiligen Aufnahmen für die Flächensteckungen hab ich mit
UHU Endfest geklebt.
Danach noch den Balsastab mit schwarzem Spray schnell lackieren und die
Fahrwerkshalterung mit Superkleber anbringen.
Für Seiten- und Höhenleitwerk
gibt es auf A3-Papier Schablonen, die ausgeschnitten werden und mit
einem wirklich scharfen Tapezieremesser aus Depron konturtreu
ausgeschnitten werden.
Seitenleitwerke oben und unten werden ebenfalls mit UHU-Por aufgeklebt
und auf der Oberseite mit weiteren Depron-Teilen (wie im Plan
gezeichnet) verstärkt.
Das Seitenruderservo wird mit Superkleber und einem kleinen
Balsaholzrest und eienr Schraube befestigt und zusätzlich mit Klebeband
am Depron gesichert.
Das Höhenleitwerk wird mit dem Höhenruderservo versehen (UHU-Por
& Klebeband), der Kohlestab am Ruder über die ganze länge
geführt (UHU-Por & Klebeband) und dann das Ruder mit Klebeband
oben und unten am Leitwerk angeschlagen.
Ruderhorn wird mit UHU-Por am Ruder aufgeklebt und ein Anlenkungsstab
aus 1mm Stahl zurechtgebogen und eingehängt. Fertig.
Auf
der Unterseite des Leitwerks ist aus 3D-gedruckten Teilen ein
Verschluss mit Superkleber am Rumpf befestigt, dessen Gegenstücke am
Höhenleitwerk mit UHU-Por befestigt sind. Somit kann das Höhenleitwerk
von hinten eingeschoben und verrieglet werden und für den Transport
auch wieder abgenommen werden. Man muss nur das Servo abstecken.
Die Gondel aus
Depronteilen wird auch mit der bewährten Kombi UHU-Por + Klebeband
gefertigt, wobei es einen Trick gibt: das 20mm breite Mittelteil,
welches von vorne oben über die Spitze, den Boden und hintenrum gebogen
wird, das würde beim Biegen brechen...ausser man bringt vorher schon
Klebeband auf der späteren Aussenseite auf. Zusätzlich wird die spätere
Innenseite mit dem Lineal mehrfach quer zur Biegerichtung mit dem
Linieal eingedrückt. dadurch wird der Teil biegsam.
Die Gondelhalterung und das damit integrierte Fahrwerk wird im Prinzip
nur aus Carbonstäben mit 2mm Durchmesser in der richtigen Länge (siehe
Zeichnung) zusammengesteckt. Die Steckverbinder kommen alle aus dem
3D-Drucker und müssen vor der Verwendung nur noch mit einem 2mm-Bohrer
korrekt gereinigt/augebohrt werden.
Beachte, dass nicht vorher Kleber angebracht wird und dann der Teil
aufgeschoben wird - das klappt nciht, weil der Kleber sofort das
Schieben verhindert. Meine Teile passen so gut "saugend" auf den
Carbonstab, sodass ein einfaches Zusammenstecken und ein Tropfen
Superkleber als "Sicherung" vollkommen reichen.
Die
Abmessungen der Carbonstäbe und die Position der einzelnen Teile kann
man aus der Grafik entnehmen:
Gewichtsbilanz:
Rumpf
mit Gondel & Leitwerken |
103
g
|
Balsastab:
23g
Kleinteile aus dem 3D-Drucker (ohne Motorträger, ohne Rippen): 20g
Rest: Depron und Kohlestäbe
|
Flächen |
92
g
|
Fläche:
je 46g
|
Fernsteuerung |
35
g
|
Empfänger,
Kabel & 4 Servos
|
Motoreinheit |
65
g
|
Motor
mit Regler: 50 g
Motorträger & Propeller: 15 g
|
Akku
(3s1p LiPo 1000 mAh) |
85
g
|
|
Summe: |
380
g
|
|
Verglichen mit der original Bleriot III (300g,
abgespeckt mit 2s 600mAh und anderen Maßnahmen sogar unter 250g) ist
das nun nicht soo umwerfend leicht. Das Gewicht wurde vor allem bei den
Flächen liegengelassen; da ist das Original nur Halb so schwer.
Für die Flächenspannweite und -tiefe ist das Gewicht aber
trotzdem ein sehr, sehr guter Wert. Die Flugeigenschaften sind
entsprechend gut!
Mit
denm verbauten Roxxy 2225 und einem 9"x4,7" Prop zieht die Maschine
nicht wirklich senkrecht nach oben, aber Hovern klappt schon...
Noch
hab ich einen 10A Regler drinnen, sodass die Maximalleistung auf
ca. 110W beschränkt ist - obwohl der Motor doch noch etwas
mehr
könnte. Aber das war ja nicht das Ziel.
Das angepeilte Ziel
"Wiesenschleichen" und Landungen in Zeitlupe, das erfüllt diese
Maschine perfekt: Man fleigt so langsam und niederig über die Wiese,
dass die Räder durch einzelne Grashalme gedreht werden...
Die
Querruder kann man wie Flaps nach unten stellen - aber da die Bleriot
sowieso schon hervorragend langsam fliegt, merkt man nur wenig
Unterschied zum Normalflug.
Fazit:
Endlich wieder eine sauber steuerbare Bleriot - "der" Slow-Flyer
schlechthin!
- und das alles zum Selbermachen, wenn man Zugriff auf einen 3D-Drucker
hat!
|
Screenshots aus Sketchup:
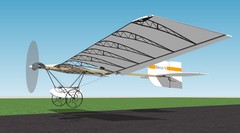
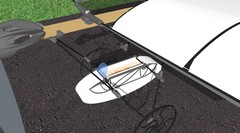

Das fertige Modell:
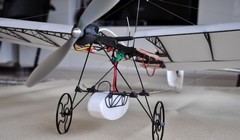
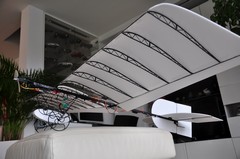
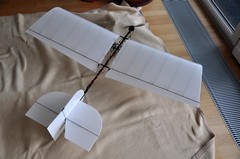
Erstflug:
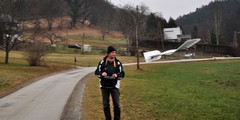
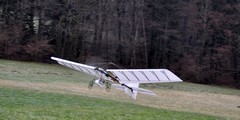
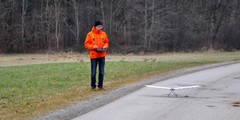
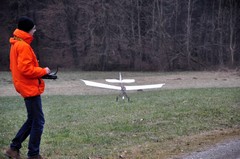
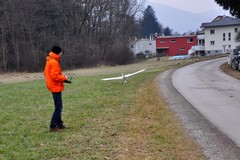
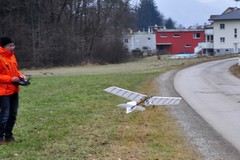
Detailfotos mit dezenterer
Verkabelung:
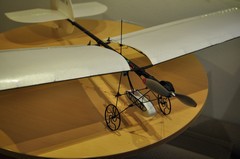
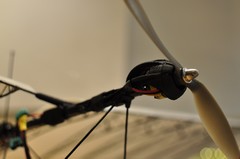
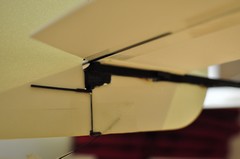
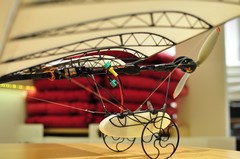
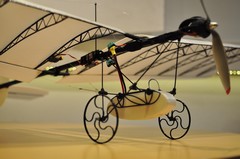
|